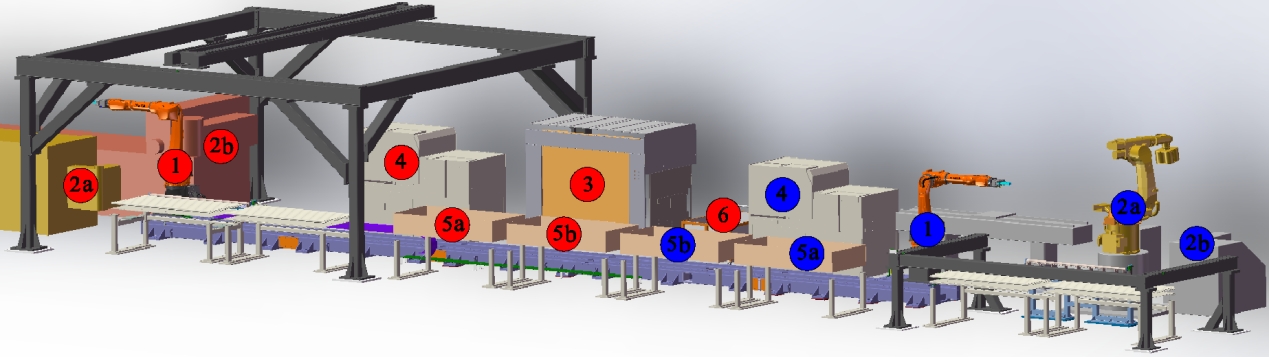
Main manufacturing stations and components of the aero-enginebending pipe production line (Image by the research group)
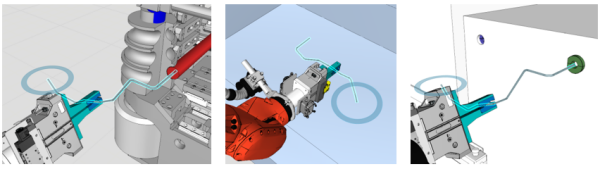
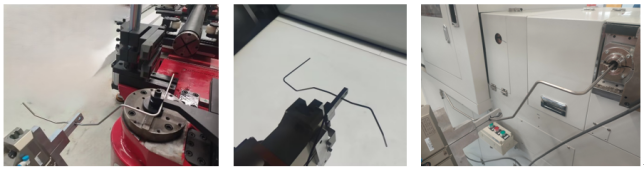
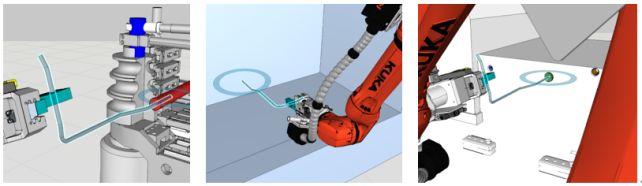
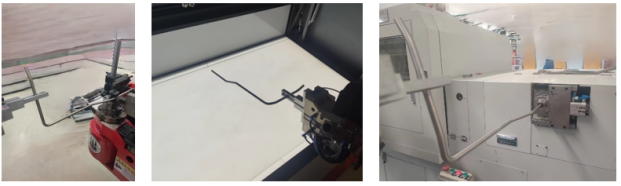
Simulation path planning and processing verification for complex bending pipes (Image by the research group)
Aero-engine bending pipes are among the most critical components in aircraft engines. They exhibit characteristics such as numerous categories, significant variations in shape and size, and low usage quantities per specific type. Their manufacturing requires multiple processes and demands high precision and specific physical properties.
Recently, a research team from the Shenyang Institute of Automation (SIA), Chinese Academy of Sciences(CAS), has developed an automated production line for aero-engine bending pipes. This line enables automated multi-station manufacturing and inspection of bending pipes with varying dimensions.
During automated production, aero-engine bendingpipes are susceptible to deformation under gravity during machining and inspection across various workstations. To address this, researchers employed finite element method simulations to establish a gravity compensation model, significantly improving machining accuracy. Simultaneously, to meet the strict production cycle requirements of the automated line, the team conducted multi-objective path optimization. This optimization balanced machining efficiency, robot energy consumption, and the suppression of damping vibration at the pipe's free end. These combined efforts have successfully realized a high-precision and high-efficiency automated manufacturing technology for bent pipes.
Simulation and experimental results demonstrate the superiority of the proposed path planning method in terms of machining accuracy, stability, and efficiency for bending pipes. It effectively suppresses vibrations induced at the free end during grasping operations while maintaining processing efficiency. Currently, the automated bending pipe production line has been put into operaration and running stable.
This research, titled Robotic aero-engine pipe grasping posture and motion planning method in multi-stage processing based on multi-objective optimization, has been published in the Journal of Manufacturing Systems, an international journal in the field of advanced manufacturing. Associate Researcher Bo Zhou from SIA is the first author. Researcher Jibin Zhao and Researcher Renbo Xia from SIA, along with Professors Hongfeng Wang and Junwei Wang from Northeastern University in Shenyang, are the corresponding authors.
Link to paper :https://www.sciencedirect.com/science/article/pii/S0278612525001219