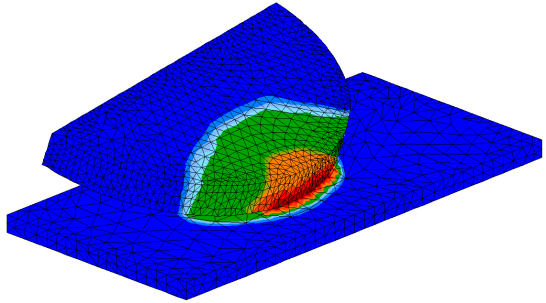
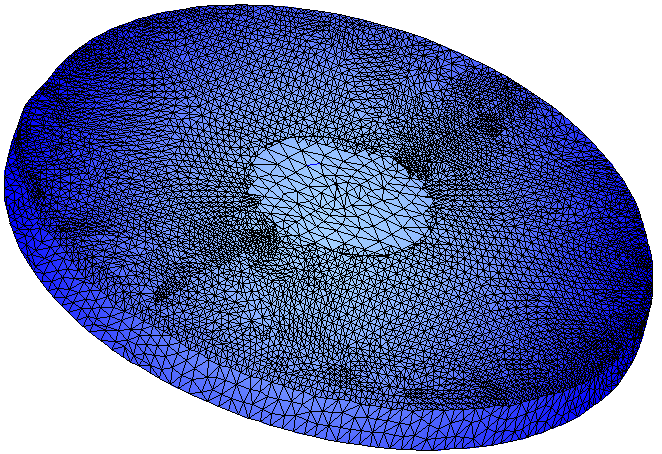
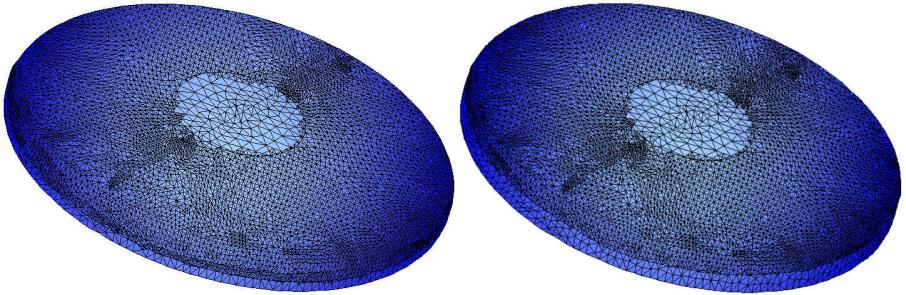
Finite element modeling and wear process analysis of rigid abrasive grinding and polishing processes (Image by the research group)
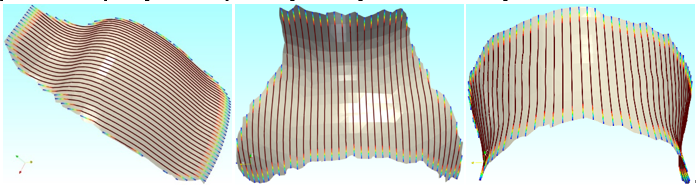
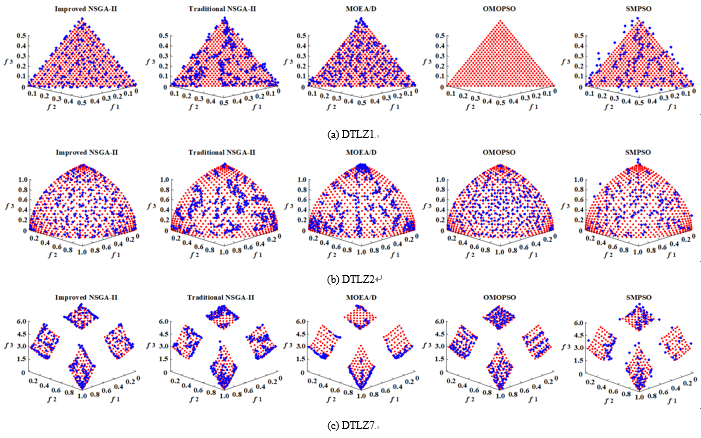
Performance comparison of the proposed optimization method for path planning of the main parts of components on a standard test set (Image by the research group)
For large-scale components such as nuclear reactor coolant pump (RCP) casings and rocket engine nozzles, characterized by complex geometries and significant dimensions, precision grinding and polishing are essential after casting and machining to ensure dimensional accuracy and required performance. Heavy-duty robots, offering high flexibility and capable of applying greater grinding pressure, present an optimal solution for the precision grinding and polishing of such workpieces.
Recently, a research team from the Shenyang Institute of Automation (SIA), Chinese Academy of Sciences(CAS), has established a robotic precision grinding and polishing system for large-scale complex curved-surface workpieces. This system is designed for the automated robotic manufacturing and inspection of the aforementioned component types.
The research team developed a physical model for disc wear during the grinding and polishing of large castings to predict tool degradation. They generated a series of geodesic offset paths characterized by the shortest path length. These paths were then converted into parameter-interpolated trajectories, further optimized in joint space for smoothness. By incorporating a multi-objective optimization function and kinematic constraints into an improved optimization algorithm, the team achieved the balanced minimization of grinding time, joint impact, and disc wear.
Simulation and experimental results validate the superiority of the proposed path planning method in terms of machining accuracy, stability, and efficiency for large castings. This approach provides new insights and solutions for the efficient utilization of rigid grinding tools, reducing tool changes, and predicting tool wear. It facilitates efficient and high-precision automated grinding and polishing for large-scale, high-accuracy, complexsurfaceworkpieces.
The research, titled Robotic disc grinding path planning method based on multi-objective optimization for nuclear reactor coolant pump casing, has been published in the Journal of Manufacturing Systems. Associate Researcher Bo Zhou from SIA is the first author and corresponding author.
Link to paper : https://www.sciencedirect.com/science/article/pii/S0278612524002474