Laser peening is an innovative surface treatment technique, and can significantly improve the mechanical performance of metallic components. To investigate the fatigue life of Ti17 titanium alloy by laser peening, laser peening experiment was undertaken using Nd:YAG laser system with the pulse-width of 15ns and max pulse-energy of 7J. Firstly, the mechanical properties and microstructure with different laser peening parameters were investigated, which were measured and observed by Vickers indenter, X-ray diffraction, scanning electron microscope and transmission electron microscope. Micro-hardness and compressive residual stress distribution was remarkably improved. High-density dislocations and fine-grains were observed in the surface layer. Then, several stress levels were chosen to be applied on the tension and compression fatigue specimens. The fatigue life and fracture mechanism of the specimens without- and with- laser peened were compared, and the strengthening mechanism was indicated by analyzing the effects on the microstructure and residual stress evolution. The results demonstrate that laser peening could effectively improve the fatigue life of Ti17 titanium alloy.
The laser energy and impact times have an influence on the roughness and residual stress value. Laser peening could generate a roughened surface with moderate increases in the values of roughness parameters, but the roughness value is not adversely affected by laser peening treatment. With the most severe laser peening conditions, the maximum compressive stress value reaches -524 MPa at a depth of about 150 μm while the surface stress reaches -492 MPa.
Dislocation walls, high density dislocations, dislocation cells and refined grain are generated by laser peening. 3 impact times are enough to generate refine grain structure in the surface of Ti17 titanium alloy, the crystals will get smaller with the increasing of impact times.
Using the most severe laser peening parameters, the maximum micro-hardness value reaches 415 HV0.2 at the material surface, similar to the distribution law of residual stress. The hardened layer depth increases significantly with laser peening impact times. The affected depth of hardness is about 550 μm for one impact times, 800 μm for 2 impact times, 950 μm for 5 impact times and 1400 μm for 10 impact times.
Laser peening is found to be very effective in lower fatigue stress level, the maximum fatigue life increases about 13.8 times at stress level of 250 MPa. The fatigue life increases with the increasing of laser energy and impact times.
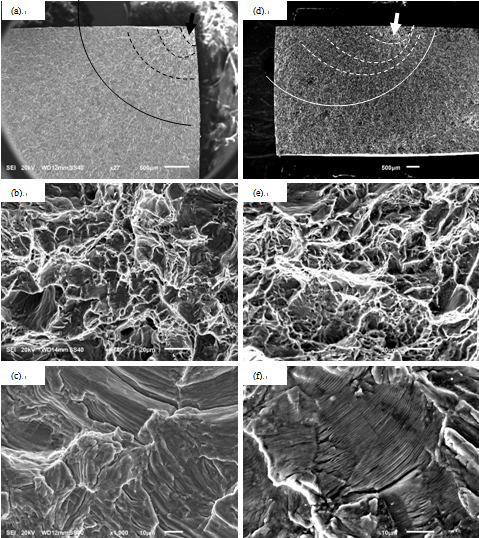
Fig. 8. Fracture morphology of specimens after fatigue test. (a), (b), (c) Fracture of specimens without laser peening; (d), (e), (f) Fracture of laser peened specimens with laser energy of 5J.
This study was co-supported by the National 863 Program (No. 2012AA041310). Papers related to this result were published on Applied Surface Science (Qiao Hongchao. Experimental investigation of laser peening on Ti17 titanium alloy for rotor blade applications [J]. Applied Surface Science, 2015, 351: 524-530 DOI: 10.1016/j.apsusc.2015.05.098).
Contact:
QIAO Hongchao
Email: hcqiao@sia.cn
Shenyang Institute of Automation Chinese Academy of Science