Atomic force microscopy (AFM) has become a promising tool for manipulating nano-objects to fabricate nano-structures or nano-devices. However, there are still some challenges facing the development of an AFM based robotic nanomanipulation system, such as the uncertainties associated with AFM tip and nanoparticles, the single point force and interaction between the tip and nanoparticles, and the parameter calibration of models being used.
To overcome the severe bottle-neck in AFM based robotic nanomanipulation system,researchers from Shenyang Institute of Automation (SIA), CAS proposed a concept of the virtual nano-hand (VNH) strategy for automatic and stable nanoparticle pushing without monitoring the dynamic interactions between the tip and nanoparticles. The VNH strategy is like a mimic of a human hand to flick a ball with multi-fingers alternatively, which prevents the tip from slipping away from the particle and stably hobbles the manipulated particle throughout the whole pushing process.
The concept of the AFM-based VNHS is illustrated in Fig 1. In the traditional target-oriented pushing (TOP), the single AFM tip is always programmed to strike the center of the nanoparticle being pushed [Fig.1 (a)]. However, this method can easily cause nanoparticles to be lost during the process of pushing, due to the uncertainties with the tip positioning. Another traditional nanoparticle pushing strategy, double-tip pushing [Fig.1(b)], can make nanoparticle pushing more stable but not flexible. In the strategy of virtual nanohand pushing, [Fig.1 (c),(d)], the single AFM tip mimics multiple tips by quickly touching different points for stable pushing of the nanoparticle or nanorod, respectively.
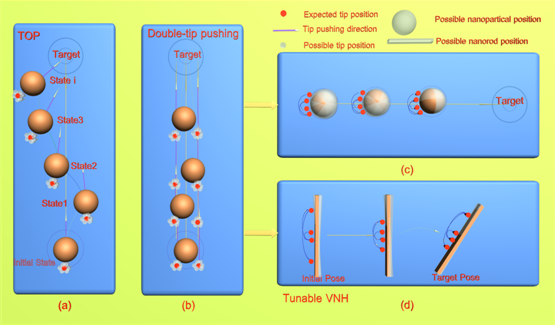
Fig.1. the concept of the virtual nano-hand. (a) Conventional Target Oriented Pushing (TOP) (b) Real double tip strategy (c)~ (d) AFM-based virtual nano-hand strategy. (Image provided by WANG Zhiyu et.al)
The VNH was designed basing a probabilistic prediction method (PPM) developed for dealing with the uncertainties in the nano-particle pushing. One of the advantages of VNH strategy is to assist the operator to perform nanoparticle transfer stably, efficiently, and effectively. Ultimately, the VNHS can intensify the AFM-based robotic nanomanipulation system so that the only thing an operator needs to do is specify the manipulation task.
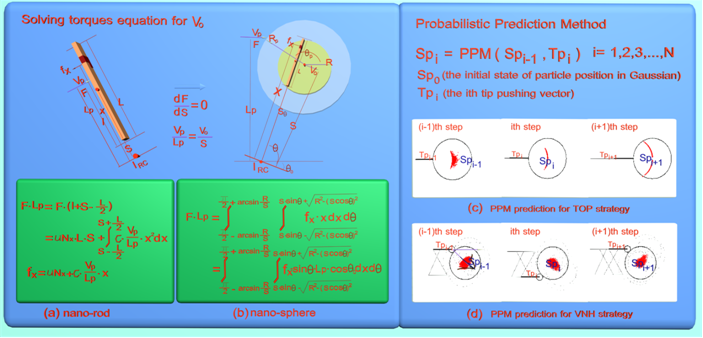
Fig. 2. The Kinematics Models of Nano-objects and the Probabilistic Prediction Method Based on Monte-Carlo Algorithm for the Position Distribution. (a) The static torques self-balanced for nano-rod pushing. (b) The torques for nano-sphere pushing. (c) The probabilistic prediction for the uncertainty distribution of particle position in TOP strategy. (d) The probabilistic prediction in VNH strategy where the uncertainty distribution can be described by beta function. (Image provided by WANG Zhiyu et.al)
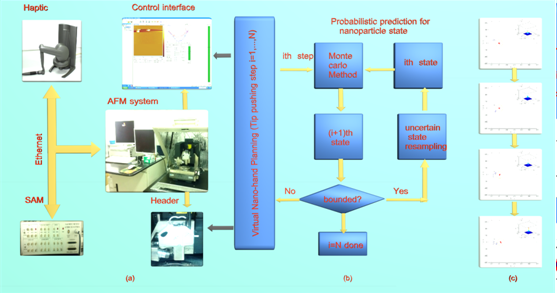
Fig. 3. Applications of the Virtual Nano-hand Strategy in AFM based Nanomanipulation System. (a) Current AFM based nanomanipulation system. (b) Virtual Nano-hand strategy predictor evaluate the adopted tip pushing trajectory. (c) Simulation results of the predictor for the probabilistic distribution of the manipulated nanoparticle positions.(Image provided by WANG Zhiyu et.al)
This work was published on IEEE Nanotechnology Magazine, Volume. 7 (4): 6-11,2013.It was supported by the National Natural Science Foundation of China (Grant No. 61327014, 61304251), and the CAS/SAFEA International Partnership Program for Creative Research Teams.
CONTACT
Wang Zhiyu
Shenyang Institute of Automation, the Chinese Academy of Sciences
Email:zywang@sia.cn