It is an effective way to take the advantages of the microgravity environment for making scientific experiments in the space station. However, due to the various types of sources producing vibration, various experimental conditions in the space station in terms of the varying acceleration are not ideal for scientific research. Vibration in the microgravity environment is with the characteristics of low frequency, small amplitude, and randomness.
Aiming at this issue, researchers from Shenyang Institute of Automation (SIA), the Chinese Academy of Sciences proposed a control method of an active vibration isolation system with parallel mechanism applied to space application, which is effective for disturbance suppression.
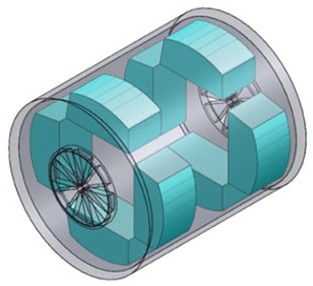
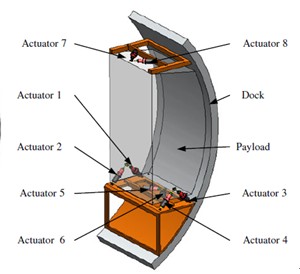
Fig. 1 The left figure is the layout of the microgravity scientific research rack in the space station section and the right The parallel active vibration isolation system of space station scientific experimental rack. (Image provided by LIU Jinguo et.al)
The layout of the sensitive experiment payload in space station for scientific research is illustrated in Fig. 1(a). According to the isolation and damping mechanism of the International Space Station (ISS) and the requirements for attenuation of vibration, a novel active vibration isolation and damping system with parallel distributed isolators is designed, which is shown in Fig. 1(b). The main features of the proposed system are as following. First, it consists of three component elements, including the cabin of space station, the platform for scientific research, and the actuators which are taken as the isolators. Moreover, the platform for scientific research is mounted on cabin of the space station isolated via eight voice coil motors in parallel mechanisms through which the systematic rigidity and reliability are increased. Finally, there are no special requirements of the characteristics for voice coil motor, and the flexure.
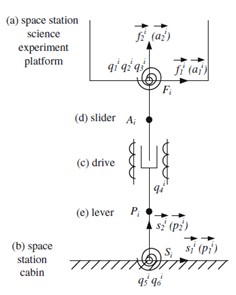
Fig. 2 The reference coordinate system (Image provided by LIU Jinguo et.al)
Model of the active isolation system for microgravity scientific research is shown in Fig.2, which consists of the following components: (a) microgravity scientific research platform, (b) cabin of the space station, and (c) several actuations. In this design, a single-axis actuator includes the slider (d) and the static lever (e). The dynamics model of active vibration isolation system with payload is represented via Kane’s method; thereafter the description in state-space linearization is introduced.
Controllability and observability of the system are checked by state-space equations of the system. The state feedback decoupling with double-loop proportional-integral-derivative (PID) control method is adopted as the system controller to design the decoupling matrix and the PID controller.
For improving the properties of the system, a control system with H-infinity method is also designed and evaluated. Finally, various types of simulation results are demonstrated to verify the effectiveness of the active vibration damping system proposed. The acceleration and angle acceleration of payload in closed-loop system with H-infinite controller is shown in Fig.3, which means the method proposed is feasible.
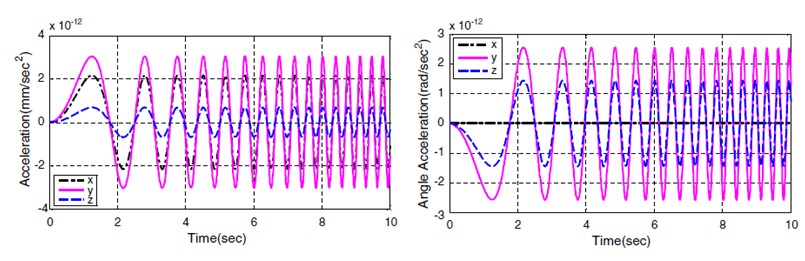
Fig. 3 Acceleration and angle acceleration of payload center-of-mass in closed-loop system with H∞ controller (Image provided by LIU Jinguo et.al)
This work is published on Nonlinear Dynamics, 2014. The research is supported by the National Natural Science Foundation of China (51175494 and 61128008), the State Key Laboratory of Robotics Fund (O8A120S), and Macao Science and Technology Development Fund (108/2012/A3).
CONTACT:
Prof. LIU Jinguo
Shenyang Institute of Automation, the Chinese Academy of Sciences
Email: liujinguo@sia.cn