The capsule endoscopy (CE) has been the most effective medical device to examine the gastrointestinal (GI) tract painlessly and non-invasively. CE has become the gold standard for the diagnosis of most diseases in the GI tract. Many researchers are engaging in developing an active CE, which can be called capsule robot, using various driving mechanisms. However, the imperfections of friction model between the capsule robot and the intestine has been one of the biggest obstacles of the development of the capsule robot. The capsule robot needs to start and stop frequently when working in the intestine. The frictional resistance increase rapidly from a small value in the robot’s starting process.
Aiming at this, researchers from Shenyang Institute of Automation (SIA), the Chinese Academy of Sciences have conducted study to figure out the intestinal frictional resistance variation in the starting process of the capsule robot when the capsule robot moves inside the intestine. Some experiments are conducted to measure the actual frictional resistance with a homemade uniaxial experiment platform. The frictional resistance is found to changes with the capsule’s velocity, acceleration and original state.
The experimental results describe the frictional resistance of the capsule at a certain velocity and acceleration. One of the experimental results is shown in Fig. 1, where the velocity is 20mm/s and the acceleration is 100mm/s2. The variation trend of the frictional resistance can be seen as an irregular trapezoid approximately according to the filtering results. The process of frictional resistance increase is similar to a straight line segment. When the capsule moves at a constant velocity, the frictional resistance fluctuates uncertainly because of the intestinal samples’ viscoelasticity and pleated surface. The frictional resistance decreases rapidly after the capsule stops because of stress relaxation phenomenon of the intestinal material. However, the frictional resistance does not decrease to zero in a long time because part of capsule’s kinetic energy converts to intestinal deformation energy.
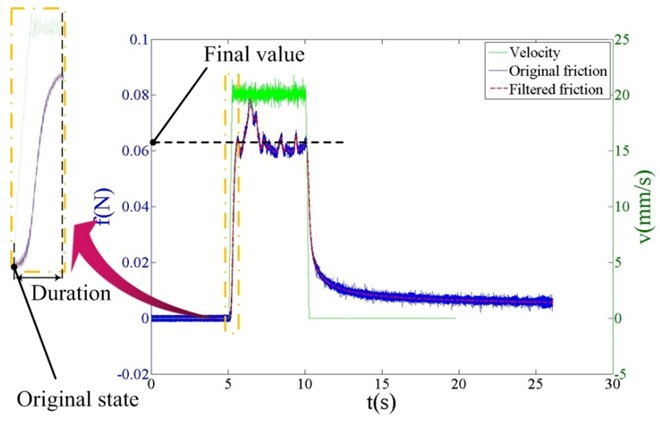
Fig. 1 Experimental results when the capsule moves at a velocity of 20mm/s and acceleration of 100mm/s2 (Image provided by ZHANG Cheng et.al)
The change of frictional resistance over time in the capsule’s starting process can be expressed by analytical expression. The formula has relations with the capsule’s velocity and acceleration. If the capsule moves from stationary state and the intestine has no deformation, it can be expressed as

If the capsule moves intermittently, the expression also has to do with the time interval between two successive motions. In other words, the original state of the frictional resistance is not zero but a changing value over time.
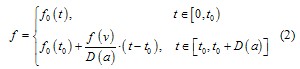
The situation described by equation is an exceptional case in practice. The capsule robot needs to start and stop frequently when working in the intestine. Therefore, the analytical expression of equation has more important practical application value. An additional experiment is conducted to test and verify the validity of the above analytical expression. The capsule is pulled by the driving unit in the intestine intermittently at a velocity of 25mm/s and acceleration of 500mm/s2. The time interval between two successive motions is 5s. Fig. 2 presents a comparison of the frictional resistance variation with respect to time between the proposed analytical expression and the experimental result.
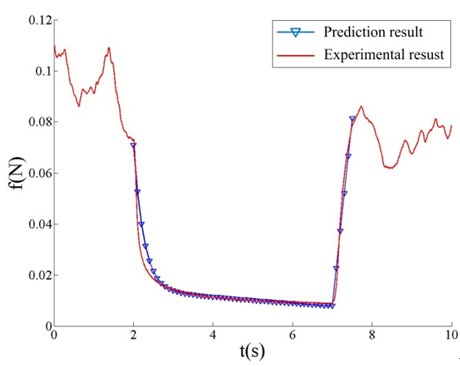
Fig. 2 Comparison of the frictional resistance variation with respect to time between the proposed analytical expression and the experimental result when the capsule moves intermittently with a velocity of 25mm/s and acceleration of 500mm/s2 (Image provided by ZHANG Cheng et.al)
The achievement of the paper will perfect the frictional resistance model of the capsule robot moving in the intestine. Then the control strategy will be optimized in the starting process of the capsule robot according to the better frictional resistance model. The motion will be smoothed and more energy will be saved in the starting process. Further, it is hoped to contribute to the development of the capsule robot in the future.
This work was published on the Tribology International, Volume 70, Feb 2014, 11-17. It was supported by the National Natural Science Foundation of China (No. 61105099) and the National Technology R&D Program of China (No. 2012BAI14B03).
CONTACT:
Dr. Cheng Zhang
State Key Laboratory of Robotics, Shenyang Institute of Automation, CAS
Email: zhangcheng@sia.cn