Laser peening technology has matured into a fully qualified production process designed to improve the performance and fatigue life of work-pieces, and will enable designers to consider higher stress levels in life limited designs. Laser peening can be used to prolong the fatigue life of aerospace, automotive, power generation, nuclear waste disposal, petroleum drilling, medical implants and recreational sports. In the aerospace industry, this surface technology starts to be applied to the tip of fan blades inside air craft engines with the aim of saving the fatigue failure by foreign object damage.
Researchers from Shenyang Institute of Automation (SIA), Chinese Academy of Sciences has developed a blisk laser peening device in 2009 (as shown in Fig.1). To improve the life of air craft engines, the device now serves in AVIC Shenyang Liming Aero-engine (Group) Corporation LTD. The device has a capability of 130 watts average power, a pulse width of 15 to 20 ns, pulse energy to 25J, a repetition rate to 4 Hz, and a nominally rectangular laser-spot profile.
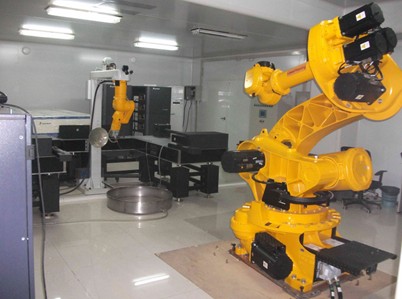
Fig.1 Blisk laser peening device developed by SIA (Image provided by Qiao Hongchao)
By using the blisk laser peening device, the researchers have recently studied the effects of laser peening on residual stress distributions and deformation microstructure of TiAl alloy. The MicroXAM-1200 3D non-contact optical profilers were used to measure the surface roughness of peened samples. Experiments show that the surface roughness of peened samples increased with higher laser energy. The effect of laser shock peening on the alloy is shown in Fig. 2.
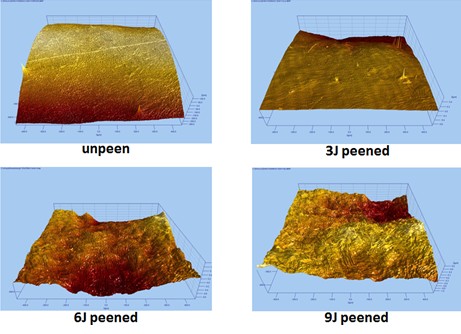
Fig.2 Surface roughness of laser peened samples increase with laser energy (Image provided by Qiao Hongchao and Zhao Yixiang)
The researchers also tested the relationship between laser peening energy and the surface Vickers hardness of sample materials. As shown in Fig.3, the virgin material has a Vickers hardness value of 286.5 HV, and the value increases to more than 340 HV with the increasing of laser peening energy accordingly. Moreover, the researchers tested the relationship between laser peening energy and the residual stress of sample materials. Convectional XRD was used to measure the residual stress values. At the beginning, the virgin material has low compressive residual stress value of -63Mpa. With higher laser peening energy, the residential stress value increase to more than 250 MPa. (As shown in Fig 4). Experiments show that, the surface roughness of laser peened TiAl samples increase with laser energy. Higher laser peening energy generates high surface hardness and compressive residual stress.
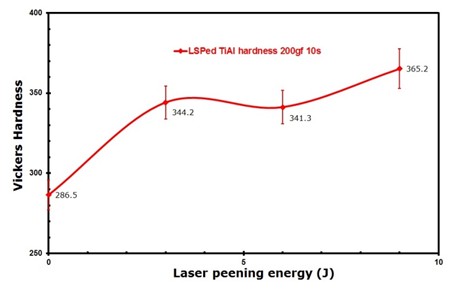
Fig.3 Surface residual stress increase with laser energy (Image provided by Qiao Hongchao and Zhao Yixiang)
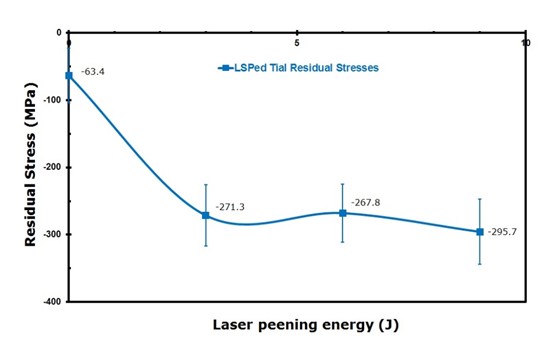
Fig.4 Surface roughness of laser peened samples increase with laser energy (Image provided by Qiao Hongchao and Zhao Yixiang)
This work was presented on the 4th International Conference on Laser Peening and Related Phenomena (ICLPRP) in Madrid in May 2013. The ICLPRP is held every two years, and is the world’s top conference on laser peening. The aim of ICLPRP is to provide a forum for the discussion of latest innovations and studies in laser peening and their application to industrial sectors among scientists and engineers from all over the world. According to the real importance of the basic physical foundations of the technique, the scope of the Conference is naturally open to include contributions relating to basic phenomena, alternative methods, residual stress measurement, etc. in order to increase the understanding of underlying physics of the technique and promote further applications.
CONTACT:
Professor: ZHAO Jibin
Associate professor: QIAO Hongchao
Shenyang Institute of Automation, Chinese Academy of Sciences
Email: hcqiao@sia.cn
Tel: 024-83601252