Laser peening is a recently-developed surface treatment method designed to improve the performance and prolong the fatigue life of work-pieces. Laser peening which generates confined plasma on the surface of work-pieces use high power density and short pulse laser irradiation. The explosion of confined plasma leads to high pressure shock wave, which causes the compressive residual stress on the surface of work-pieces. Since 1970s, considerable attention has been paid to potential application of laser peening in the aviation industry and other industrial fields. However, the effect of laser radiation on materials and phenomenon near radiation point are not so understood. Although residual stress is most commonly used to evaluate the effects of laser peening, residual stress in depth direction is measured after electrochemical polishing which is one of the fracture evaluations, and the offline test efficiency is lower. Several online detection methods are used to evaluate the effects of laser peening, such as PVDF, thermal energy method, fundamental frequency method and so on. However, these methods have problems that it is applicable only to thin simple work-pieces.
To solve this problem, researchers from Shenyang Institute of Automation (SIA), Chinese Academy of Sciences developed acoustic emission method (AEM) which is one of the nondestructive efficient detection methods to evaluate the effects of laser peening. The online quality detection system developed by SIA is mainly composed of acoustic emission receiver, amplifier, laser detector, data acquisition card, industrial computer and monitor. The online quality detection system is shown in Fig.1. Acoustic emission receiver can respond to the laser plasma shock wave whose frequency range is 100 to 400 KHz. Laser detector is used to detect the pulse laser and convert it into an electrical pulse signal which is used as external synchronization trigger signal of synchronous data acquisition system to collect sensor signal. Synchronous data acquisition card achieve external trigger of sensor signal, synchronous acquisition and storage and real-time signal processing. Industrial computer mainly achieve processing of data, filtering and calculations, as well as historical queries. Monitor display the results of every laser peening.
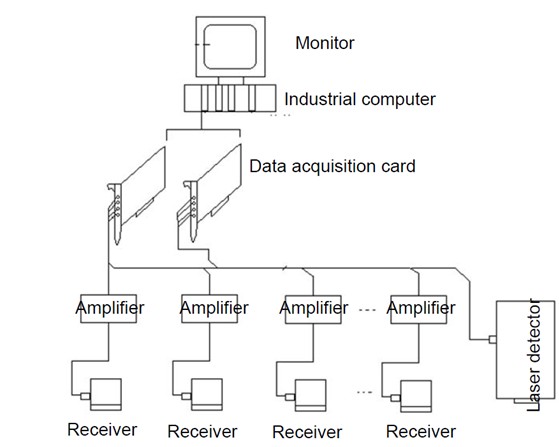
Fig.1 Schematic diagram of online quality detection system (Image provided by Qiao Hongchao, et. al)
The photos of acoustic emission receiver developed at SIA are shown in Fig.2 and Fig.3. The receiver is made of stainless steel, and contains 3 acoustic emission sensors. The 3 acoustic emission sensors, which are mounded on the back of the receiver, intervals 120 degrees, distributed on the circumference of diameter 120 mm. In order to prevent the spread of the sound wave, there is a rubber pad between receiver and standoffs.
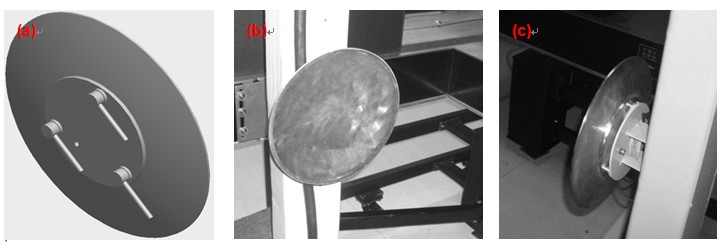
Fig.2 Photos of acoustic emission receiver (Image provided by Qiao Hongchao, et. al)
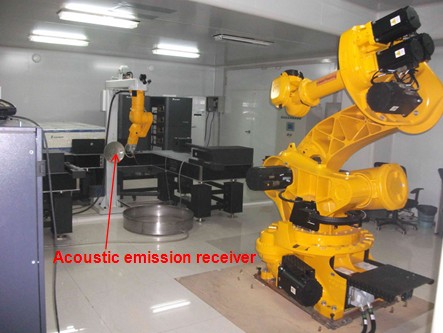
Fig.3 Photos of laser peening device which is developed at SIA (Image provided by Qiao Hongchao, et. al)
Laser peening produce high-intensity pressure shock wave. part of the shock wave propagate into the work-piece, compressive stress layer is formed in the surface the action of shock wave, part of the shock wave spread to the outside of the work-piece, spread into the air medium. There is a relationship between the signal amplitude, signal energy, ringing count of the shock wave and the shock effect, so we can assess the effect of laser peening by detecting shock wave waveform feature, and derive formula 1. Sound pressure level factor is twenty times the size of the logarithm of the arithmetic mean of the product of ringing count, signal amplitude and signal energy.
Lf: Sound pressure level factor
Coui: Ring count of the ith acoustic emission channel
Ampi: Signal amplitude of the ith acoustic emission channel
Eni: Signal energy of the ith acoustic emission channel
The experiment results are shown in Fig.4. Before laser peening, its surface residual stress is 0 MPa. When the single pulse energy is 0J, sound pressure level factor is 0 dB. When the single pulse energy is increased to 3J, the surface compressive residual stress is 100MPa, and the sound pressure level factor increase to 95 dB. When the single pulse energy is increased to 5J, the surface compressive residual stress is 250MPa, and the sound pressure level factor increase to 236 dB. Experiments results show that online detection system used for laser peening is responsive and reliable.
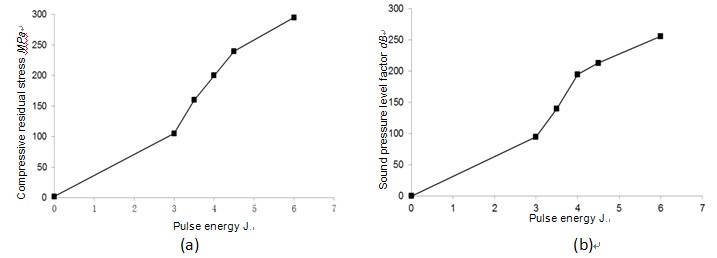
Fig.4 (a) Effect of single pulse energy on surface residual stress, (b) Effect of single pulse energy on sound pressure level factor (Image provided by Qiao Hongchao, et. al)
The online detection system has been successfully applied in the SIA-LSP-10-2 laser peening device. The SIA-LSP-10-2 laser peening device was developed at SIA in 2009, and now serves in AVIC Shenyang Liming Aero-engine (Group) Corporation LTD.
This work was presented on the 4th International Conference on Laser Peening and Related Phenomena (ICLPRP) in Madrid, Spain in May 2013. The ICLPRP is held every two years, and is the world’s top conference on laser peening. The aim of ICLPRP is to provide a forum for the discussion of latest innovations and studies in laser peening and their application to industrial sectors among scientists and engineers from all over the world. According to the real importance of the basic physical foundations of the technique, the scope of the Conference is naturally open to include contributions relating to basic phenomena, alternative methods, residual stress measurement, etc. in order to increase the understanding of underlying physics of the technique and promote further applications.
CONTACT:
Professor: ZHAO Jibin
Associate professor: QIAO Hongchao
Shenyang Institute of Automation, Chinese Academy of Sciences
Email: hcqiao@sia.cn
Tel: 024-83601252